I prodotti "Best Sellers" per un'azienda manifatturiera non sono sempre i prodotti che si vendono di più, ma quelli che fanno più utili, ovvero che ti fanno guadagnare meglio, ma sei sicuro di saperli individuare?
Mentre è molto facile contare il numero di pezzi prodotti per ogni articolo non è altrettanto facile invece capire su quali prodotti si ha la marginalità più alta e questa valutazione è tanto più complessa tanto più è complesso il processo produttivo.
Non si deve cadere nel tranello mentale di dire, ad esempio:
Con questo pezzo guadagno circa 40 € perchè lo vendo a 50 € ed ha me costa 6 € di materia prima e 2 minuti di tempo ciclo su una macchina che vendo a 120 €/h (2€/min) operatore incluso, ovvero 4 €.
Non mi riferisco soltanto al fatto che si devono sommare anche i costi indiretti di gestione (amministrazione, pulizie, commerciale...) ma mi sto riferendo proprio al calcolo dei costi diretti che è grossolanamente errato. Il costo orario delle macchine e degli impianti (al netto della quota parte degli operatori che ci lavorano) è un valore che non è mai fisso e può essere calcolato soltanto a posteriori o a fronte di una pianificazione.
Il "costo orario fisso" va bene nella fase di preventivazione, ma a consuntivo, oltre all'effettivo tempo impiegato, si deve verificare anche il reale costo orario sostenuto.
Cerchiamo di capire, almeno intuitivamente, perchè il costo orario deve essere calcolato a consuntivo lasciando poi a strumenti software dedicati, come iProd, l'esecuzione di tutti i complessi calcoli che ci stanno dietro.
Il costo orario REALE di una macchina è noto solo al termine di una commessa ed è uguale al rapporto tra il "Costo Totale di Possesso e Disponibilità" e le "Ore lavorate" per la commessa specifica.
IL COSTO TOTALE DI POSSESSO e DISPONIBILITA' =
LEASING/AMMORTAMENTO + MANUTENZIONI + ENERGIA ELETTRICA + UTENSILI
ATTENZIONE alla parola DISPONIBILITA': ci vuole ricordare che i costi devono essere calcolati non solo per il periodo in cui la macchina è stata impegnata nella commessa, ma DAL MOMENTO IN CUI ha terminato la commessa PRECEDENTE!
Lo avete mai fatto così? Forse no ed ecco il risultato che si ottiene simulando due lotti produttivi della durata di 4 o 8 ore lavorate al variare del tempo trascorso dall'ultimo utilizzo della stessa macchina. Da 32 €/ di costo orario per un uso continuativo, 8 ore al giorno per 5 giorni a settimana si può arrivare a quasi 400 €/h se abbiamo un periodo di non utilizzo di due settimane continuative (cosa tutt'altro che rara).
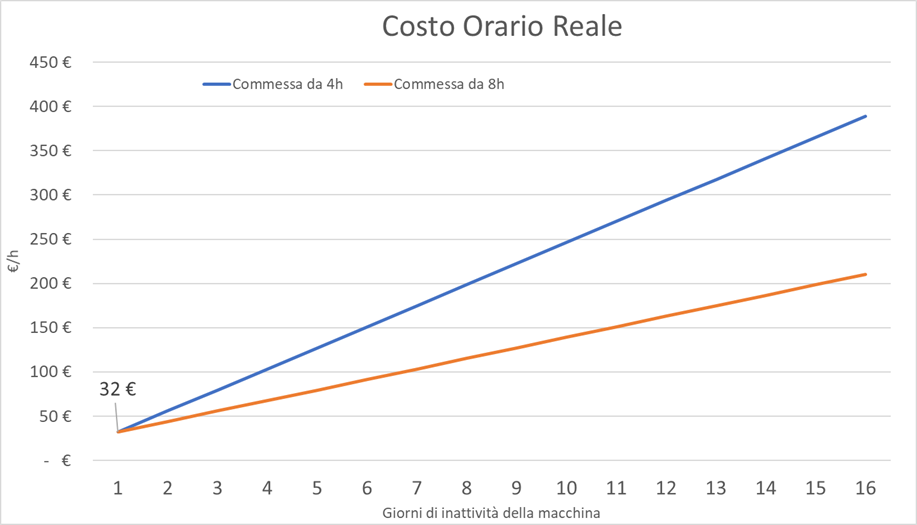
Quali sono quindi i tuoi prodotti Best Seller?
NON TI SENTI PIU' TANTO SICURO DELLA TUA RISPOSTA INIZIALE... HAI RAGIONE A DUBITARE, NON HAI GLI STRUMENTI PER RISPONERE SU DUE PIEDI
Se moltipliche questa incertezza per ogni macchinario che impieghi per poter produrre ogni componente che vendi scoprirai che non è affatto semplice capire quali sono i tuoi prodotti più remunerativi ma sicuramente è più facile capire quelli che sicuramente non lo sono:
- Vengono fatti in modo sporadico,
- Utilizzano molti macchinari o utensili dedicati che per la gran parte del tempo restano inutilizzati in attesa che arrivi una "commessa giusta"
- Nonostante tutto questo calcoli il costo di vendita sulla base del "costo orario standard"
Raggiungi l'eccellenza produttiva, usa iProd anche tu
Se vuoi veramente sapere quali sono i tuoi costi di produzione non puoi affidarti all'intuito ed all'esperienza ma devi passare a strumenti informatici capaci di acquisire in modo continuo come usi i tuoi macchinari.
Prova subito iProd, la piattaforma innovativa che ha permesso già a molte aziende come la tua di raggiungere l'eccellenza produttiva con la semplicità di un'App.
Inizia Gratis registrandoti su www.app.iprod.it e segui le indicazioni passo-passo.